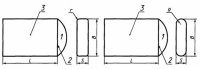
МЕЖГОСУДАРСТВЕННЫЙ СТАНДАРТ
СЛИТКИ ИЗ АЛЮМИНИЯ И АЛЮМИНИЕВЫХ
ДЕФОРМИРУЕМЫХ СПЛАВОВ ПЛОСКИЕ
ДЛЯ ПРОКАТА
Технические условия
ГОСТ 9498-79
МЕЖГОСУДАРСТВЕННЫЙ СТАНДАРТ
СЛИТКИ ИЗ АЛЮМИНИЯ И АЛЮМИНИЕВЫХ
ДЕФОРМИРУЕМЫХ СПЛАВОВ ПЛОСКИЕ
ДЛЯ ПРОКАТА
Технические условия
Flat ingots of aluminium and wrought aluminium alloys for rolling. Specifications
ГОСТ
9498-79
Дата введения 01.01.80
Настоящий стандарт распространяется на плоские слитки, отлитые из алюминия и алюминиевых деформируемых сплавов методом полунепрерывного или непрерывного литья и предназначенные для прокатки на листы, ленты и другие полуфабрикаты.
Стандарт полностью соответствует СТ СЭВ 831-86.
(Измененная редакция, Изм. № 3, 4).
1. СОРТАМЕНТ
1.1. Форма и размеры слитков из алюминия и алюминиевых деформируемых сплавов должны соответствовать черт. 1 или 2 и табл. 1 и указываться в заказе-наряде.
1 — донник; 2 — мнимая линия; 3 — донная часть
Черт. 1 Черт. 2
Радиус закругления ребер r (черт. 1) должен быть не более 20 мм, R (черт. 2) — не более 445 мм.
По согласованию изготовителя с потребителем допускается замена плюсовых предельных отклонений по толщине и длине слитков на минусовые и изменение формы донника. Донником (для необрезанных слитков) считается (черт. 1 и 2) часть слитка, расположенная на расстоянии не более 200 мм от торца слитка до мнимой линии, измеряемом по середине широкой грани слитка.
Таблица 1*
* Таблица 2. (Исключена, Изм. № 4).
Размеры, мм
Толщина S
Ширина В
Длина L
Номинальная
Предельное отклонение
Номинальная
Предельное отклонение
Предельное отклонение
литье в кристаллизатор скольжения
литье в электромагнитный кристаллизатор
литье в кристаллизатор скольжения
литье в электромагнитный кристаллизатор
для слитков мерной длины
для слитков немерной длины
От 100 до 200 включ.
+5
—
От 400 до 800 включ.
+7
-4
—
+20
+150
Св. 800
+10
-5
—
+30
Св. 200 до 450 включ.
+6
±10
Св. 800 до
1300 включ.
+10
-5
+20
-5
Св. 1300
±10
+25
-5
Св. 450 до 600 включ.
+9
±15
От 1000 до 1300 включ.
±10
+20
-5
Св. 1300
+15
-10
+25
-10
(Измененная редакция, Изм. № 1, 2, 4).
1.2, 1.3. (Исключены, Изм. № 4).
1.4. Длина слитка определяется без учета донника.
(Измененная редакция, Изм. № 4).
2. ТЕХНИЧЕСКИЕ ТРЕБОВАНИЯ
2.1. Слитки изготовляют в соответствии с требованиями настоящего стандарта по технологической инструкции, утвержденной в установленном порядке.
Слитки изготовляют из алюминия по ГОСТ 11069-74 и алюминиевых сплавов марок АД0, АД1, АМг2, АМг3, АМц, ММ по ГОСТ 4784-97 и марки AMг1M1 с химическим составом в соответствии с табл. 3. Химический состав слитков может быть установлен по согласованию с потребителем.
Таблица 3
Обозначение
Химический состав, %
Алюминий
Железо
Кремний
Медь
Цинк
Титан
Магний
Марганец
Прочие, каждой в отдельности
Сумма примесей
A1Mг1M1
Основной компонент
0,7
0,7
0,25
0,2
0,2
0,8-1,3
1,0-1,5
0,05
0,15
При производстве слитков из алюминия технической чистоты допускается введение модификатора титана или титан плюс бор в количестве до 0,02 % для алюминия марки А8 и до 0,03 % для алюминия марок А7, А6, А5 и А0. По согласованию изготовителя с потребителем допускается увеличение массовой доли титана до 0,05 %. Содержание модификатора не учитывается в общей сумме примесей при определении марки алюминия.
Массовая доля натрия в сплавах АМг2, Амг3 и АМгМ1 не должны быть более 0,001 %.
В слитках алюминия технической чистоты по ГОСТ 11069 отношение примесей железа к кремнию должно быть не менее 1. К обозначению марки такого металла добавляется буква П. При цветной маркировке добавляется наклонная полоса того же цвета, что и вертикальные полосы. По требованию потребителя допускается производство слитков с отношением примесей железа к кремнию менее 1.
В слитках из алюминия всех марок, предназначенных для изготовления посуды, содержание свинца не должно быть более 0,15 %, мышьяка — 0,015 %.
Слитки, предназначенные для производства тонкой фольги, изготовляются из алюминия марок А5 и А6, с отношением содержания железа к кремнию не менее 1,5.
(Измененная редакция, Изм. № 1, 4, 5).
2.2. Слитки для производства фольги, предназначенной для изготовления:
— высокоемких электролитических конденсаторов, отливаются из алюминия на основе марки А99 с массовой долей примесей железа 0,003-0,006 %, кремния 0,003-0,006 %, меди не более 0,005 %, цинка не более 0,002 %, титана не более 0,001 %, суммой примесей не более 0,020 % и обозначаются А99КВ;
— оксидных низкоемких конденсаторов, отливаются из алюминия на основе марки А99 с массовой долей примеси меди не более 0,005 % и обозначаются А99КН.
(Измененная редакция, Изм. № 1).
2.3. Для получения проката со специальными свойствами по согласованию изготовителя с потребителем допускается легирование алюминия добавками, содержание которых указывается в документе о качестве и не учитывается при определении марки алюминия.
2.4. Слитки поставляются без обрезки торцов и фрезерования поверхности. По согласованию изготовителя с потребителем допускается поставка слитков с обрезанными торцами, разрезанных на мерные части с фрезерованной поверхностью, а также слитков в гомогенизированном состоянии.
Слитки, предназначенные для изготовления тонкой фольги, поставляются с обрезанной донной частью на 250-50 мм и литниковой частью на 150-30 мм.
2.5. Слитки должны иметь однородную структуру. В слитках не должно быть раковин, трещин, газовых пузырей, пористости и расслоений.
На макрошлифах поперечных сечений слитков не допускаются включения площадью более 1 мм2 каждое в количестве, приведенном в табл. 4.
Таблица 4
Размеры слитка, мм
Допустимое количество включений на макрошлифе поперечного сечения слитка, шт.
алюминий
алюминиевые сплавы
Толщина до 200 включ., ширина до 800 включ.
2
3
Толщина св. 200 до 400 включ., ширина св. 800 до 1600 включ.
3
5
Для слитков толщиной более 400 мм, шириной более 1200 мм допускаемое количество включений на макрошлифе поперечного сечения слитка устанавливается по согласованию с потребителем.
Для слитков, предназначенных для производства тонкой фольги марок А6 и А5, величина штрихдефектов не должна быть более 0,5 мм/см2.
В необработанной краевой зоне слитков из алюминиевых деформируемых сплавов допускается наличие пор глубиной, не превышающей значений, приведенных в табл. 5.
(Измененная редакция, Изм. № 1, 3, 4, 5).
2.6. Необработанная поверхность слитков должна быть без раковин, трещин, неслитин и посторонних включений.
На малых гранях и ребрах слитков допускаются вмятины от захватов подъемного механизма.
(Измененная редакция, Изм. № 2, 4).
2.7. Допускаемые дефекты поверхности слитков (наплывы, неслитины на закруглениях ребер, вырубки и следы зачистки, вмятины) не должны превышать приведенных в табл. 5.
Таблица 5
Толщина слитков, мм
Высота (глубина) дефектов поверхности, мм
слитки из алюминия
слитки из алюминиевых сплавов
литье в кристаллизатор скольжения
литье в электромагнитный кристаллизатор
До 200 включ.
3
—
—
Св. 200
5
4
2
По требованию потребителя высота (глубина) дефектов поверхности слитков из алюминия не должна превышать 2 мм для слитков толщиной до 200 мм включительно, 3 мм — для слитков толщиной свыше 200 мм.
Для слитков из алюминиевых сплавов, отлитых в электромагнитный кристаллизатор, допускается волнистость с высотой волны не более 5 мм.
(Измененная редакция, Изм. № 2, 3, 4).
2.8. В донной части необрезанных слитков на расстоянии не более 150 мм от мнимой линии (черт. 1 или 2) не должно быть: пережимов глубиной более 15 мм в слитках из алюминия и алюминиевых сплавов; трещин длиной более 70 мм и шириной более 3 мм, наплывов высотой более 8 мм в слитках из алюминиевых сплавов.
Допускаются трещины, неслитины, наплывы, следы вырубки и зачистки на доннике слитков из алюминия и алюминиевых сплавов (черт. 1 или 2).
2.9. Литниковая поверхность необрезанных слитков не должна иметь пористости и посторонних включений.
Глубина усадочной раковины не должна превышать 15 мм — для слитков толщиной до 300 мм включ.; 30 мм — для слитков толщиной свыше 300 мм до 450 мм включ.; 60 мм — для слитков толщиной свыше 450 мм до 600 мм включ.
Допускаются следы вырубки и зачистки, окисные плены на литниковой поверхности.
2.8, 2.9. (Измененная редакция, Изм. № 2, 4).
2.10. Кривизна по длине слитка (по узкой и широкой граням) не должна быть более 5 мм на 1 м длины, по требованию потребителя — 3 мм на 1 м длины.
Кривизна по длине слитков, используемых для производства тонкой фольги, не должна быть более 3 мм на 1 м длины.
(Измененная редакция, Изм. № 1, 2).
2.11. Косина реза слитков с обрезанными торцами или разрезанных на мерные части шириной до 800 мм включительно не должна превышать 10 мм, для слитков шириной до 1500 мм включительно — 15 мм и для слитков шириной свыше 1500 мм — 20 мм.
(Измененная редакция, Изм. № 2).
2.12. Содержание водорода в расплаве при литье слитков не должно быть более:
0,17 см3/100 г металла для алюминия;
0,25 см3/100 г металла для сплава АМц;
0,30 см3/100 г металла для сплава ММ;
0,35 см3/100 г металла для сплавов АМг2 и AMг1M1;
0,40 см3/100 г металла для сплава АМг3.
(Измененная редакция, Изм. № 4).
2.13-2.13.1. (Исключены, Изм. № 4).
2.13.2. (Исключен, Изм. № 2).
2.13.3. (Исключен, Изм. № 4).
2.14. Скручиваемость плоских слитков устанавливается по требованию потребителя.
(Введен дополнительно, Изм. № 3).
2а. Требования безопасности
2а.1. Алюминий и его сплавы в виде слитков малотоксичны, пожаро- и взрывобезопасны.
2а.2. Алюминий и его сплавы относятся к веществам 3-го класса опасности по ГОСТ 12.1.005-88, ГОСТ 12.1.007-76 и при воздействии на организм являются умеренно опасными веществами преимущественно фиброгенного действия. При вдыхании паров пыли алюминия и его сплавов могут поражаться верхние дыхательные пути и легкие, раздражаться слизистые носа, рта, глаз, а также развиваться экземы и дерматиты.
Предельно допустимая концентрация аэрозолей алюминия и его сплавов (в пересчете на алюминий) в воздухе рабочей зоны (ПДКр.з) — 2 мг/м3.
2а.3. Алюминий и его сплавы в виде слитков электропроводны, не следует допускать контакта продукции с проводами, находящимися под электрическим напряжением.
2а.4. В условиях производства необходимо соблюдать правила общей и личной гигиены и безопасности труда, избегать вдыхания пыли и паров расплавленного металла, попадания в глаза и на кожу. При работе следует применять средства индивидуальной защиты: респираторы — по ГОСТ 12.4.028-76, пылезащитную одежду — по ГОСТ 12.4.099-80 и ГОСТ 12.4.100-80, очки — по ГОСТ 12.4.013-85*. При работе со слитками из алюминия и алюминиевых сплавов на пунктах длительного хранения применение специальных средств защиты не требуется.
_____________
* На территории РФ действует ГОСТ Р 12.4.013-97.
При переплаве слитков или переработке отходов должно быть обеспечено высушивание слитков и отходов перед загрузкой в плавильную печь.
(Раздел 2а введен дополнительно, Изм. № 5.)
2б. Требования охраны окружающей среды
2б.1. При соблюдении правил хранения и транспортирования алюминий и его сплавы в виде слитков не оказывают вредного воздействия на окружающую среду.
2б.2. Вредное воздействие на окружающую среду может происходить в результате сбросов и выбросов загрязняющих веществ в процессе производства, при возникновении чрезвычайных ситуаций (пожар, взрыв, наводнение).
При попадании алюминия и его сплавов в виде слитков в водоемы, при воздействии на них агрессивных веществ (кислота, щелочь) возможно выщелачивание алюминия с образованием алюминатов, оказывающих токсическое воздействие на флору и фауну.
2б.3. Среднесуточная предельно допустимая концентрация в воздухе населенных мест (ПДКсс) алюминия и его сплавов не регламентирована, оксида алюминия (в пересчете на алюминий) — 0,01 мг/м3.
Предельно допустимая концентрация алюминия в воде водных объектов хозяйственно-питьевого и культурно-бытового пользования (ПДКв) — 0,5 мг/л.
Предельно допустимая концентрация алюминия в воде рыбохозяйственных водоемов (ПДКв.р) — 0,04 мг/л.
2б.4. Некондиционную продукцию и отходы должны возвращать в производство (переплав).
(Раздел 2б введен дополнительно, Изм. № 5.)
3. ПРАВИЛА ПРИЕМКИ
3.1. Слитки предъявляют к приемке партиями. Партия должна состоять из слитков одного размера и одной марки алюминия или сплава.
В партии, предназначенной для производства тонкой фольги, должно быть не более трех слитков, отлитых параллельно.
Партия слитков сопровождается документом о качестве, содержащим:
— товарный знак или наименование и товарный знак предприятия-изготовителя;
— марку алюминия или сплава (для слитков, предназначенных для производства фольги из алюминия марок А5 и А6, дополнительно указывается отношение примесей железа к кремнию);
— номер партии;
— номера плавок;
— номера слитков в плавке;
— массу партии;
— количество слитков;
— результаты определения химического состава каждой плавки, содержание водорода и величину штрихдефектов (для плавок, в которых они определялись);
— обозначение настоящего стандарта.
(Измененная редакция, Изм. № 1, 2, 4).
3.2. Контролю размеров и качества поверхности должен подвергаться каждый слиток партии. Контролю кривизны и перпендикулярности плоскости реза подвергают 10 % слитков от партии, но не менее двух слитков.
Скручиваемость слитков определяют на двух слитках от партии.
(Измененная редакция, Изм. № 1, 3).
3.3. Контролю химического состава подвергают 3 % слитков партии, но не менее двух слитков от каждой партии и одного слитка от каждой плавки.
На предприятии-изготовителе для контроля химического состава отбирают пробы от жидкого металла каждой плавки из летки разливочной печи.
(Измененная редакция, Изм. № 1).
3.4. Массовую долю натрия при литье слитков из алюминия определяют периодически, но не реже одного определения на 100 плавок. По требованию потребителя определение натрия производится один раз в сутки из каждой разливочной печи.
(Измененная редакция, Изм. № 4).
3.5. Для контроля радиуса закругления ребер, внутренних дефектов и штрихдефектов отбирают не менее трех слитков на 100 плавок. Определение проводят периодически по требованию потребителя.
(Измененная редакция, Изм. № 2).
3.6. Содержание водорода при литье слитков из алюминия определяют периодически, но не менее одного определения в сутки из каждой разливочной печи на пробах, отобранных из жидкого металла.
Содержание водорода в слитках, предназначенных для производства тонкой фольги, определяют для каждой партии слитков на пробах, отобранных из жидкого металла из желоба после рафинирования.
(Измененная редакция, Изм. № 1, 4).
3.6а. Содержание водорода в слитках из сплавов АМц, ММ, АМг2, АМг3 и AMг1M1, а также массовую долю натрия в слитках из сплавов АМг2, АМг3, AMг1M1 определяют в каждой плавке и указывают в документе о качестве.
(Введен дополнительно, Изм. № 4).
3.7. При получении неудовлетворительных результатов испытаний хотя бы по одному из показателей по нему проводят повторное испытание на удвоенной выборке, взятой от той же партии. Результаты повторных испытаний распространяются на всю партию.
4. МЕТОДЫ ИСПЫТАНИЙ
4.1. Длина слитка измеряется рулеткой по ГОСТ 7502 или линейкой по ГОСТ 427 от литниковой части по узкой грани до донника.
Ширина и толщина слитка измеряется рулеткой по ГОСТ 7502 или линейкой по ГОСТ 427. Ширина слитка измеряется в торце литниковой части по центральной оси. Толщина слитка измеряется в двух точках в торце литниковой части на расстоянии 150-200 мм от узких граней линейкой по ГОСТ 427. Каждое из измерений должно соответствовать (табл. 1).
Кривизну слитка определяют при помощи стальной проволоки диаметром не менее 0,2 мм по ГОСТ 2771, натянутой без провисания и прикладываемой вдоль слитка от литниковой части до точки, отстоящей на 150 мм от мнимой линии донника (черт. 1 или 2). Измеряется максимальное отклонение проволоки от поверхности слитка (?1) в миллиметрах металлической линейкой по ГОСТ 427, штангенглубиномером по ГОСТ 162 или щупами по НТД. Кривизна слитка вычисляется делением полученного значения отклонения в миллиметрах на длину измеряемой части слитка, выраженную в метрах.
(Измененная редакция, Изм. № 1, 2, 4, 5).
Черт. 4*
* Черт. 3. (Исключен, Изм. № 4).
4.2. Для проверки глубины или высоты неровностей, неслитин и наплывов на поверхности слитков должен применяться глубиномер индикаторный по ГОСТ 7661 или штангенглубиномер по ГОСТ 162. Для проверки перпендикулярности плоскости реза продольной оси слитка применяют металлический угольник по ГОСТ 3749 и измерительную линейку по ГОСТ 427. Допускается применение других измерительных инструментов, обеспечивающих соответствующую точность.
Косина реза (?2) определяется отклонением линии реза по широкой грани от прямого угла (черт. 4). Отклонение плоскости реза от прямого угла выражают в миллиметрах.
(Измененная редакция, Изм. № 1, 2).
4.3. Осмотр поверхности слитков производят без применения увеличительных средств.
4.4. Контроль внутренних дефектов проводят на макрошлифах поперечных темплетов слитков. Темплеты должны вырезаться на расстоянии, равном и превышающем толщину слитка от торца литниковой части и мнимой линии донника. Допускается проводить контроль внутренних дефектов на макрошлифах только у потребителя.
Для изготовления макрошлифов темплеты подвергают механической обработке. Шероховатость обработанной поверхности Rz должна быть не более 20 мкм по ГОСТ 2789.
Травление макрошлифов проводят 10-20 %-ным раствором едкого натра в течение 10-30 мин при комнатной температуре не ниже 15 °С. После травления поверхность темплета тщательно промывают водой и осветляют 25-50 %-ным раствором азотной кислоты до удаления темного налета с последующей промывкой в воде. Осмотр макрошлифа проводят без применения увеличительных средств.
Для контроля штрихдефектов из центральной части поперечных темплетов вырезают образцы размером 50?100 мм.
Образцы нагревают до температуры 380-400 °С, после чего осаживают по длине со степенью деформации 70-75 % и разрезают пополам перпендикулярно широкой плоскости. Полученные поверхности механически обрабатывают. Шероховатость обработанной поверхности должна быть не более 20 мкм по ГОСТ 2789. Поверхность травят 20 %-ным раствором едкого натра в течение 40-50 мин при комнатной температуре 30-40 °С.
Размеры штрихов определяют при помощи штангенциркуля по ГОСТ 166 без применения увеличительных средств.
Величину штрихов определяют делением суммарной длины штрихов в миллиметрах на площадь макрошлифа в см2.
Допускается проверка внутренних дефектов ультразвуком и горячей прокаткой по методике, согласованной между изготовителем и потребителем.
(Измененная редакция, Изм. № 1, 2, 4, 5).
4.5. Проверку химического состава проводят по ГОСТ 12697.1 — ГОСТ 12697.12, ГОСТ 3221, ГОСТ 23189, ГОСТ 11739.6, ГОСТ 11739.7, ГОСТ 11739.11 — ГОСТ 11739.13, ГОСТ 11739.15, ГОСТ 11739.20, ГОСТ 11739.21, ГОСТ 11739.24, ГОСТ 7727, ГОСТ 25086.
Допускается определять химический состав другими методами, не уступающими по точности указанным выше.
При разногласиях в оценке химического состава анализ проводят по ГОСТ 12697.1 — ГОСТ 12697.12, ГОСТ 3221, ГОСТ 23189, ГОСТ 11739.6, ГОСТ 11739.7, ГОСТ 11739.11 — ГОСТ 11739.13, ГОСТ 11739.15, ГОСТ 11739.20, ГОСТ 11739.21, ГОСТ 11739.24, ГОСТ 7727, ГОСТ 25086.
(Измененная редакция, Изм. № 1, 2, 4, 5).
4.6. Отбор и подготовку проб для определения химического состава проводят по ГОСТ 24231 и ГОСТ 3221, для слитков из алюминия высокой чистоты — с последующей отмывкой стружки спиртом и двукратным отмагничиванием железа.
(Измененная редакция, Изм. № 2, 4).
4.7. Содержание водорода определяют по ГОСТ 21132.0 или ГОСТ 21132.1. При разногласиях в оценке содержания водорода определение проводят по ГОСТ 21132.1.
(Измененная редакция, Изм. № 4, 5).
4.8. Скручиваемость слитков определяют по ГОСТ 26877.
(Введен дополнительно, Изм. № 3).
5. МАРКИРОВКА, УПАКОВКА, ТРАНСПОРТИРОВАНИЕ И ХРАНЕНИЕ
5.1. На торце каждого слитка должны быть нанесены следующие данные:
— товарный знак или наименование и товарный знак предприятия-изготовителя;
— номер плавки;
— номер слитка (не проставляется, если плавка состоит из одного слитка);
— марка алюминия или марка сплава.
Номер плавки и номер слитка наносится металлическим клеймом. Высота букв и цифр должна быть не менее 10 мм. Остальные обозначения наносятся металлическим клеймом или несмываемой краской.
(Измененная редакция, Изм. № 1, 2, 4).
5.2. (Исключен, Изм. № 1).
5.3. Слитки массой до 590 кг транспортируют в пакетах массой не более 3 т. Формирование пакетов слитков проводят по НТД. Каждый пакет должен быть скреплен обвязками, количество которых зависит от массы пакета. Для пакетов массой не более 1 т количество обвязок должно быть не менее 4; для пакетов массой не более 2 т — не менее 6; для пакетов массой не более 3 т — не менее 8.
В качестве материалов для средств скрепления пакетов применяют алюминиевую катанку диаметром не менее 9 мм по ГОСТ 13843 или другой нормативно-технической документации, или стальную отожженную проволоку диаметром не менее 6 мм по ГОСТ 3282. Масса алюминиевой катанки, применяемой для обвязки пакетов, входит в массу нетто пакета и партии.
Средства скрепления пакетов не предназначены для захвата пакетов при выполнении погрузочно-разгрузочных работ.
Слитки массой по 500 кг и более не пакетируют.
Слитки и пакеты слитков перевозят железнодорожным, морским и автомобильным транспортом в соответствии с правилами перевозки грузов, действующими на транспорте данного вида.
Железнодорожным транспортом слитки массой не более 500 кг и пакеты слитков массой не более 1 т транспортируют в крытых вагонах.
Слитки массой более 500 кг, а также пакеты слитков массой более 1 т транспортируют на открытом подвижном составе.
Размещение и крепление грузов, перевозимых по железной дороге, должно соответствовать правилам перевозки и крепления грузов, утвержденным Министерством путей сообщения.
Подготовка слитков к перевозке морским транспортом — в соответствии с ГОСТ 26653.
(Измененная редакция, Изм. № 1, 2, 5).
5.4. Транспортная маркировка слитков или пакетов — по ГОСТ 14192.
(Измененная редакция, Изм. № 5).
5.5. Алюминиевые слитки хранят в крытых складских помещениях. Допускается хранение слитков технической чистоты на открытых площадках.
(Измененная редакция, Изм. № 1).
ИНФОРМАЦИОННЫЕ ДАННЫЕ
1. РАЗРАБОТАН И ВНЕСЕН Министерством цветной металлургии СССР
РАЗРАБОТЧИКИ
А.А. Костюков, канд. техн. наук; М.Б. Гохштейн, канд. техн. наук; Е.Н. Абросимова
2. УТВЕРЖДЕН И ВВЕДЕН В ДЕЙСТВИЕ Постановлением Государственного комитета СССР по стандартам от 11.10.79 № 2410
3. Стандарт полностью соответствует СТ СЭВ 831-86
4. ВЗАМЕН ГОСТ 9498-71
5. ССЫЛОЧНЫЕ НОРМАТИВНО-ТЕХНИЧЕСКИЕ ДОКУМЕНТЫ
Обозначение НТД, на который дана ссылка
Номер пункта
Обозначение НТД, на который дана ссылка
Номер пункта
ГОСТ 162-90
4.1, 4.2
ГОСТ 11739.12-98
4.5
ГОСТ 166-89
4.4
ГОСТ 11739.13-98
4.5
ГОСТ 427-75
4.1, 4.2
ГОСТ 11739.15-99
4.5
ГОСТ 2771-81
4.1
ГОСТ 11739.20-99
4.5
ГОСТ 2789-73
4.4
ГОСТ 11739.21-90
4.5
ГОСТ 3221-85
4.5
ГОСТ 11739.24-98
4.5
ГОСТ 3282-74
5.3
ГОСТ 12697.1-77 — ГОСТ 12697.12-77
4.5
ГОСТ 3749-77
4.2
ГОСТ 13843-78
5.3
ГОСТ 4784-97
2.1
ГОСТ 14192-96
5.4
ГОСТ 7502-98
4.1
ГОСТ 21132.0-75
4.7
ГОСТ 7661-67
4.2
ГОСТ 21132.1-98
4.7
ГОСТ 7727-81
4.5
ГОСТ 23189-78
4.5
ГОСТ 11069-74
2.1
ГОСТ 24231-80
4.6
ГОСТ 11739.6-99
4.5
ГОСТ 25086-87
4.5
ГОСТ 11739.7-99
4.5
ГОСТ 26653-90
5.3
ГОСТ 11739.11-98
4.5
ГОСТ 26877-91
4.8
6. Ограничение срока действия снято по протоколу № 4-93 Межгосударственного Совета по стандартизации, метрологии и сертификации (ИУС 4-94)
7. ИЗДАНИЕ с Изменениями № 1, 2, 3, 4, утвержденными в июне 1984 г., июле 1987 г., октябре 1987 г., июне 1989 г. (ИУС 11-84, 12-87, 2-88, 11-89)
СОДЕРЖАНИЕ
1. Сортамент 1
2. Технические требования 2
2а. Требования безопасности
2б. Требования охраны окружающей среды
3. Правила приемки 4
4. Методы испытаний 5
5. Маркировка, упаковка, транспортирование и хранение 6